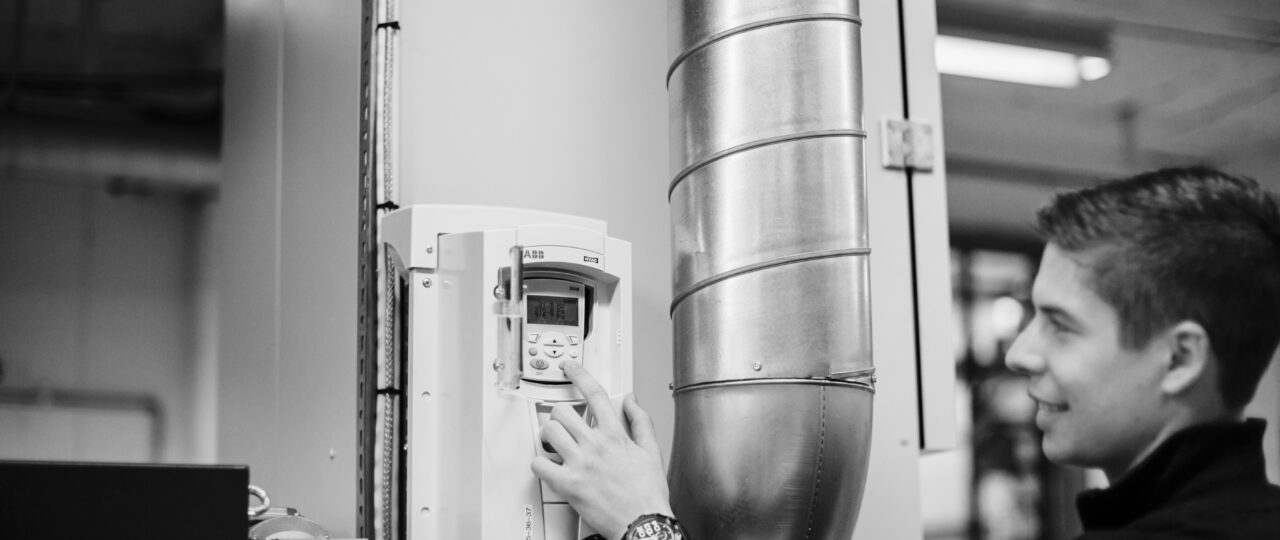
Our nose is fantastic at sensing a variety of pollutants at low levels. Polluted air is often perceived as trapped and smelly. The nose is also an excellent “filter” for large particles. They simply get caught by the nasal hairs and can often be blown out.
The particles we see in a room when the sun is shining through a window are also very large, about 70 microns in diameter. These are also some of the smallest things a human eye can see.
If we look at the particles formed in metalworking machines like lathes and grinders, they are a lot smaller. Unfortunately, these small particles can neither be sensed by our eyesight nor by our nose. No wonder, considering that an oil mist particle is the same size as a bacteria, about 3 micrometers in diameter. In machines where the spindle rotates very fast or where you need to keep a high pressure on the cutting fluid, even smaller particles are formed. We call them oil smoke particles and compare to about the same size as viruses, approximately 1 micron in diameter or less.
Both oil mist and oil smoke particles are so small that not only are they completely invisible to the eye, they also easily pass through the nose “filters” and penetrate our respiratory tracts. The smallest ones can even reach our bloodstream. Therefore, it is extremely important to keep these particles inside the machine tool, always preventing them from leaking out. The best way is to make sure the filter unit connected to the machine tool ensures a constant high level of cleaning, combined with a constant air extraction from the machine tool.
New recommendation for oil mist in Swedish industry
As previously mentioned, the Swedish Occupational Health Authority (Arbetsmiljöverket) has issued a recommendation that oil mist levels at work should not exceed 0,2 mg/m3. We believe it is the lowest level in the world. To meet this recommendation, high demands are put on both the filtering capacity and the filter extraction capacity. It is important that both can be kept constant over time, not only when the filter unit is new or recently cleaned.
For example, a HEPA H13 filter is probably a must. Otherwise, it would become extremely difficult to guarantee that filter efficiency remains constant over time. In order to obtain an acceptable service interval, a high-efficiency filtration prior to the HEPA filter must be in place, otherwise the maintenance cost may be high.
Secondly the extraction, or airflow as we call it, must remain constant over time. A filter unit that drops in extraction capacity, for example when the filter gets clogged or dirty, cannot be accepted. If it did, the contaminated air would not be extracted from the machine tool. Instead of being safely taken care of by the filter unit, the contamination that previously was inside the machine would leak out into the room.
How do you know if your machine tool has enough extraction or filtration?
Today, there are plenty of simple devices for household use that measure air temperature and humidity in our homes. There are also those that measure CO2 and particle levels. Unfortunately, there is no similar “simple” equipment for measuring oil mist and oil smoke at work. If you want to know, you would need to measure with a particle meter device. If you do not have one yourself, we can support and measure it for you. This way, we together can ensure that the machine does not leak contaminated air to your workplace. Afterwards you will receive a comprehensive report on the situation. Contact us today and we will help you examine your air quality at work!